How Tolerance Analysis Software Helps Businesses Reduce Manufacturing Costs
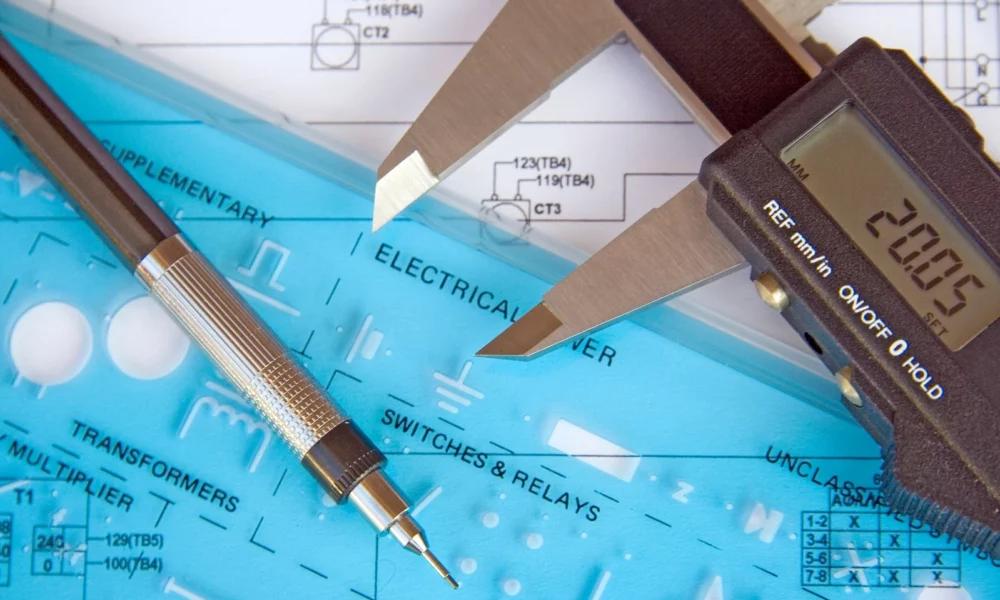
Introduction
Manufacturing processes involve several stages, from product design to final assembly. One of the major challenges in production is ensuring that components fit together as intended without excessive waste or costly rework. Tolerance analysis software plays a crucial role in managing these variations by predicting potential issues before manufacturing begins.
This article explores how businesses can use tolerance analysis software to reduce manufacturing costs while maintaining quality and efficiency.
Tolerances refer to the permissible limits of variation in a product’s dimensions or assembly. Manufacturers set these limits to ensure that parts fit together without defects while minimizing production costs. If tolerances are too tight, machining expenses increase. If they are too loose, assembly failures can occur.
Tolerance analysis software helps engineers predict the effects of variations in component dimensions before production. It enables them to simulate real-world scenarios and make adjustments to the design or manufacturing process. This proactive approach helps businesses maintain quality without unnecessary costs.
How Tolerance Analysis Software Reduces Manufacturing Costs
1. Identifying Design Flaws Before Production
One of the biggest cost factors in manufacturing is rework caused by design errors. If a product is not manufactured within the required tolerances, it may need adjustments or replacements, leading to higher expenses.
By running simulations, engineers can see how different tolerance levels affect the final product. This helps in making informed decisions about design changes before materials and resources are used.
2. Reducing Scrap and Material Waste
Material costs contribute significantly to manufacturing expenses. If components do not meet specifications, they may become unusable, leading to high scrap rates. Tolerance analysis software helps businesses determine optimal tolerances that minimize waste.
When variations in dimensions are analyzed before production, manufacturers can adjust their processes to ensure that fewer defective parts are produced. This approach reduces material wastage and lowers overall costs.
3. Optimizing Production Tolerances
Finding the right balance between tight and loose tolerances is crucial for cost efficiency. If tolerances are too strict, production costs increase due to the need for precision machining. If they are too loose, assembly issues may arise, requiring additional labor and rework.
Tolerance analysis software helps businesses determine the best tolerance range for each component. By setting optimal limits, manufacturers can reduce production costs while maintaining product reliability.
4. Improving Assembly Efficiency
Misalignment and poor fit are common issues in manufacturing that lead to delays and extra labor costs. Tolerance analysis software predicts how different parts will fit together under various conditions.
By using simulation tools, businesses can ensure that components align correctly before they reach the assembly stage. This reduces assembly errors, minimizes downtime, and improves overall efficiency.
5. Enhancing Quality Control
Defective products lead to warranty claims, customer dissatisfaction, and potential recalls. Quality control measures help prevent these issues, but manual inspection alone is not always effective.
Tolerance analysis software integrates with quality control processes by providing data-driven insights into potential defects. It helps manufacturers maintain consistency in product dimensions and assembly, reducing the likelihood of defects reaching customers.
6. Reducing Labor and Rework Costs
Manufacturing defects often require additional labor to fix issues, increasing operational costs. If a component does not meet the required tolerance, workers may need to adjust or replace it, leading to extra work hours and production delays.
Tolerance analysis software helps businesses avoid these problems by ensuring that parts meet the right specifications before production begins. By reducing rework, companies can optimize labor efficiency and maintain smooth operations.
Automation in Tolerance Analysis
Many modern tolerance analysis tools integrate with CAD and manufacturing systems, allowing for automated checks. This automation reduces the need for manual inspection, freeing up engineers to focus on more critical tasks. It also minimizes human errors that could lead to costly mistakes.
7. Streamlining Supplier Communication
Many businesses rely on third-party suppliers for parts and materials. Variations in component dimensions can lead to compatibility issues during assembly. Without a clear understanding of tolerance limits, suppliers may produce parts that do not fit properly, leading to delays and additional costs.
Tolerance analysis software allows businesses to communicate precise specifications to suppliers. By sharing tolerance data and simulations, manufacturers can ensure that all components meet the required standards. This reduces the risk of receiving defective parts and improves supply chain efficiency.
Standardizing Tolerance Data
Some tolerance analysis tools offer standardized reporting features, allowing businesses to document and share tolerance information with suppliers. This ensures consistency across different production batches and reduces the likelihood of defects.
8. Enhancing Product Reliability
A product with poor fit or misalignment may fail to perform as expected, leading to warranty claims, repairs, or recalls. These issues not only increase costs but also damage a company’s reputation.
By using tolerance analysis software, businesses can improve product reliability by ensuring that all components function as intended. Simulations help engineers identify potential weaknesses in design and manufacturing processes, reducing the risk of product failures.
Long-Term Cost Savings
Although tolerance analysis software requires an initial investment, the long-term savings outweigh the costs. Businesses that implement these tools can reduce warranty claims, extend product lifespans, and improve customer satisfaction, leading to higher profitability over time.
9. Supporting Continuous Improvement
Manufacturing processes evolve over time, and businesses must continuously improve their operations to stay competitive. Tolerance analysis software provides valuable insights that help manufacturers refine their processes and enhance efficiency.
By analyzing production data, businesses can identify trends and areas for improvement. Adjustments to tolerances, material selection, and assembly processes can be made based on real-world performance, leading to better cost management.
Data-Driven Decision Making
Tolerance analysis software generates detailed reports on component variations and manufacturing performance. These insights enable businesses to make informed decisions about process optimization, reducing costs while maintaining quality.
Conclusion
Tolerance analysis software is a valuable tool for businesses looking to reduce manufacturing costs. By identifying design flaws early, minimizing material waste, optimizing tolerances, and improving assembly efficiency, manufacturers can achieve significant cost savings.
Additionally, these tools streamline supplier communication, enhance product reliability, and support continuous improvement efforts. Investing in tolerance analysis software helps businesses maintain high-quality standards while reducing production expenses, ultimately leading to greater profitability and operational efficiency.
Source: How Tolerance Analysis Software Helps Businesses Reduce Manufacturing Costs